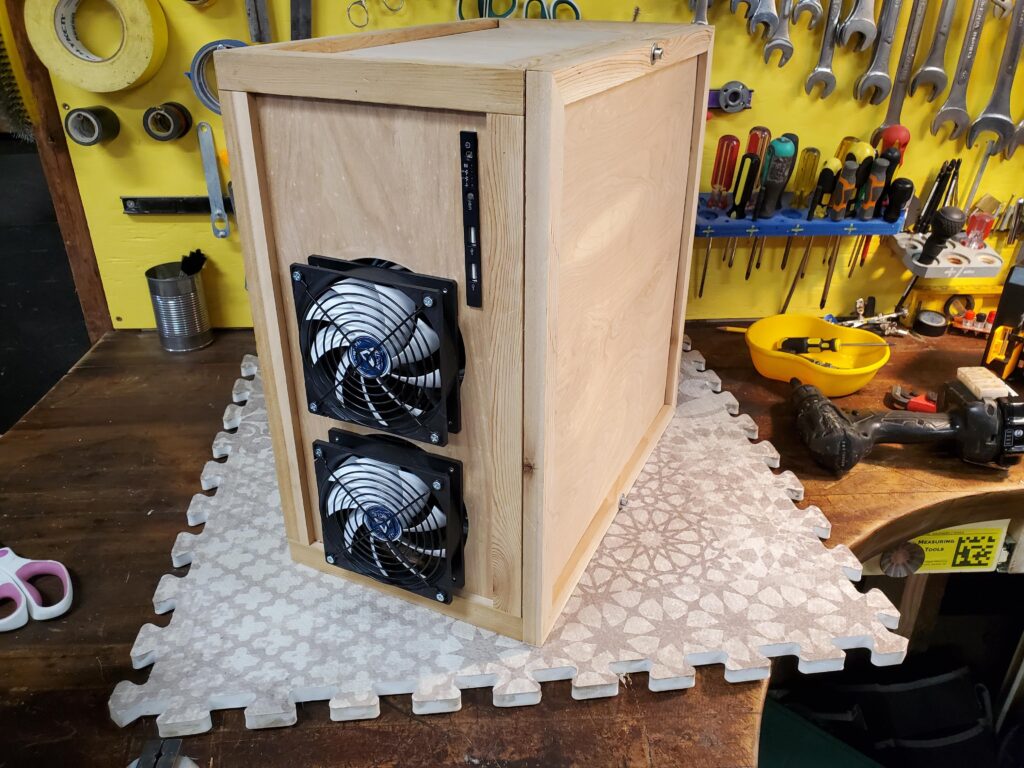
1U HP DL120 G7 servers will not boot with their fans disconnected from their proprietary motherboard headers. The original 40mm fans are actually two fans stacked; designed to have both running, but the server will still boot if one dies. iLO3 sees each fan group as 2 fans, a fan number (3-6 in my case) and an ‘A’ and ‘B’ fan.
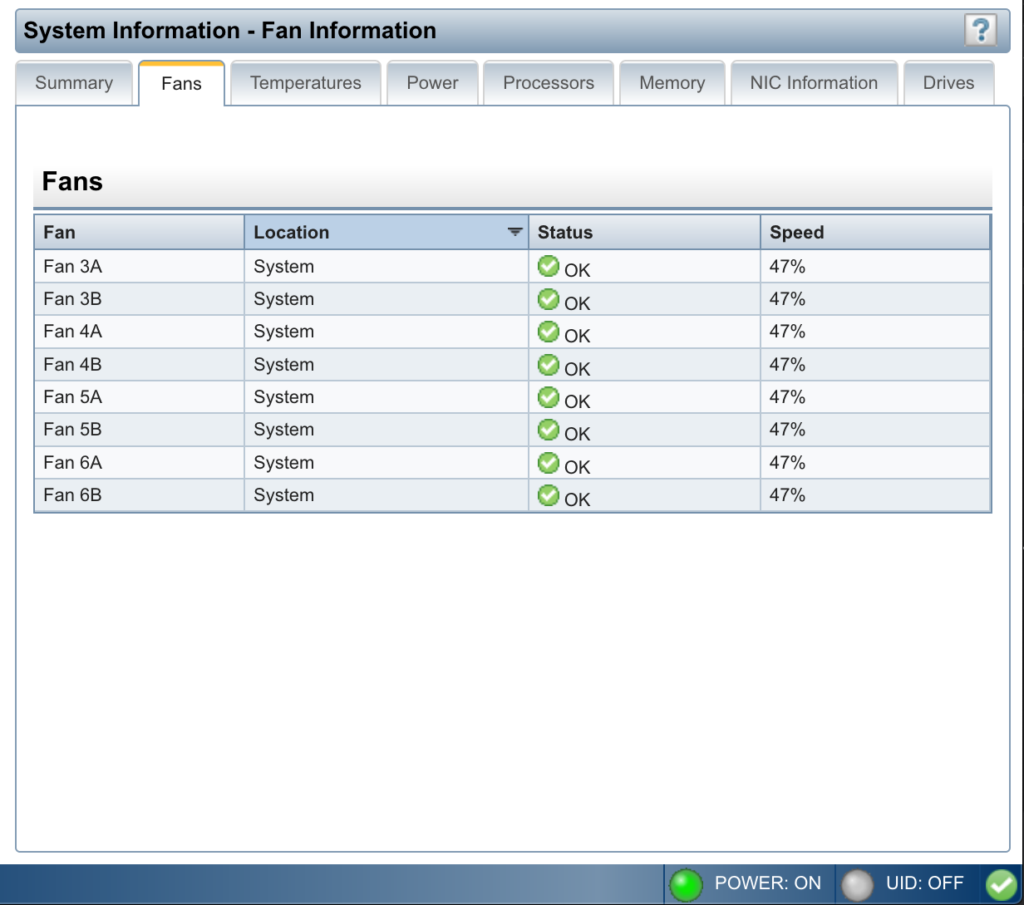
The G7 Fan connector comes both in the ‘new’ way, a 2×3 6-pin header (G8 reportedly only has these) and the ‘old’ way (which is what all 4 of mine originally were) with a 1×6 6-pin header.
Key | |
---1----2----3----4---
Typical | Blk Red Wht Blu |
Alternative | Yel Red |
Intel HSF | blk Yel Grn Blu |
----------------------
GND 12v Tach PWM
Standard PWM case fan 4-pin:
1×6 6-pin header G7 Fan Connector:
Key | |
---1----2----3----4----5----6---
| Org Blk Red Blu Yel Grn | Wire Color 1
| Grn* Wht | Wire Color 2
--------------------------------
12v GND 12v 1.6v .7v 1.6v
FanB FanA RPMa PWM RPMb
If you wire two fans to each 1×6 connector, sharing the GND and the PWM signal, you’ll satisfy the system’s need to see fans to boot. You’ll also get variable speed fans depending on temperature. I my experience, the system doesn’t care about the RPMs, it just needs to know they’re spinning. Good thing because the 120mm fans generally spin nowhere near the 7000-9000 RPMs most 1U 40mm fans spin at.
Inspired by this forum post regarding G8 servers in particular: Faking the fan signal – Microserver Gen 8 – RESET Forums (homeservershow.com)
Here are a few photos of this in action. I sourced GND and 12v+ elsewhere on the board, so in the 2 connections you see the most I’m only connected to RPMa, RPMb and PWM. I’m using some (sparsely populated) 2.54mm spacing JST-XH connectors and a terminal block
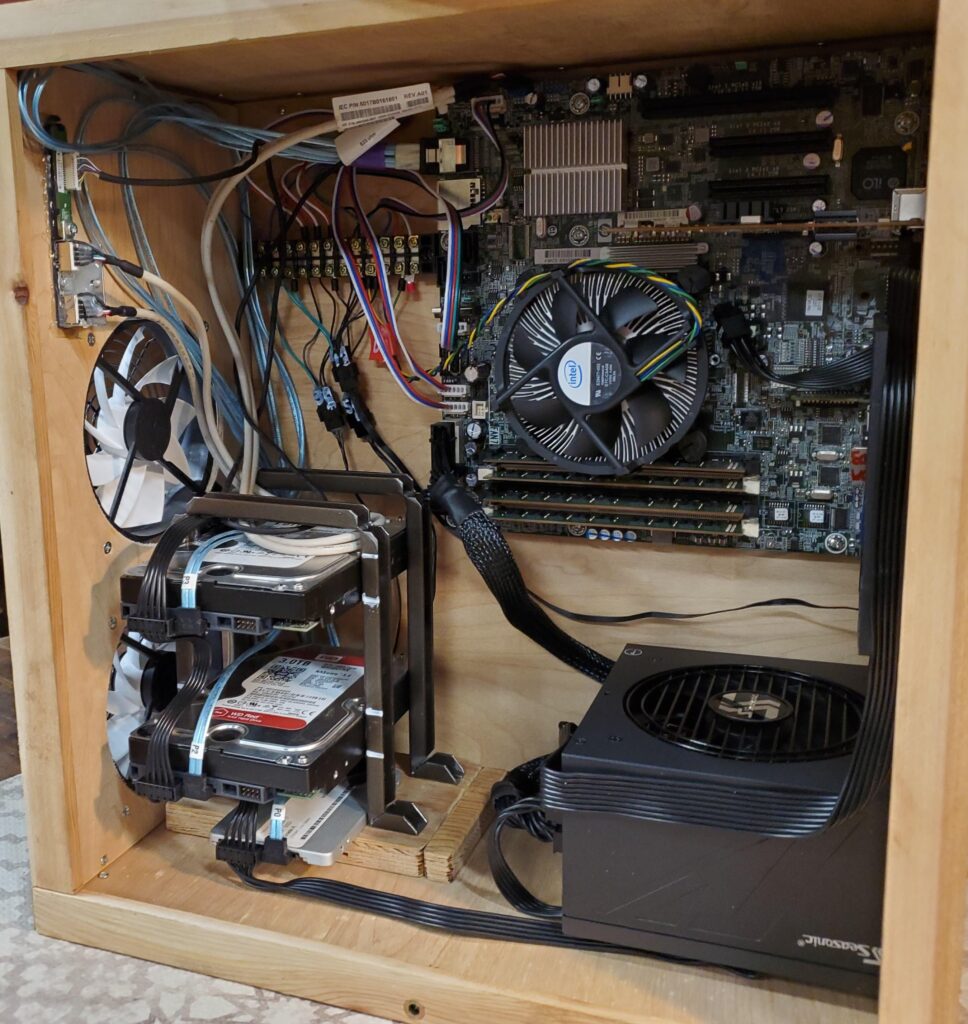